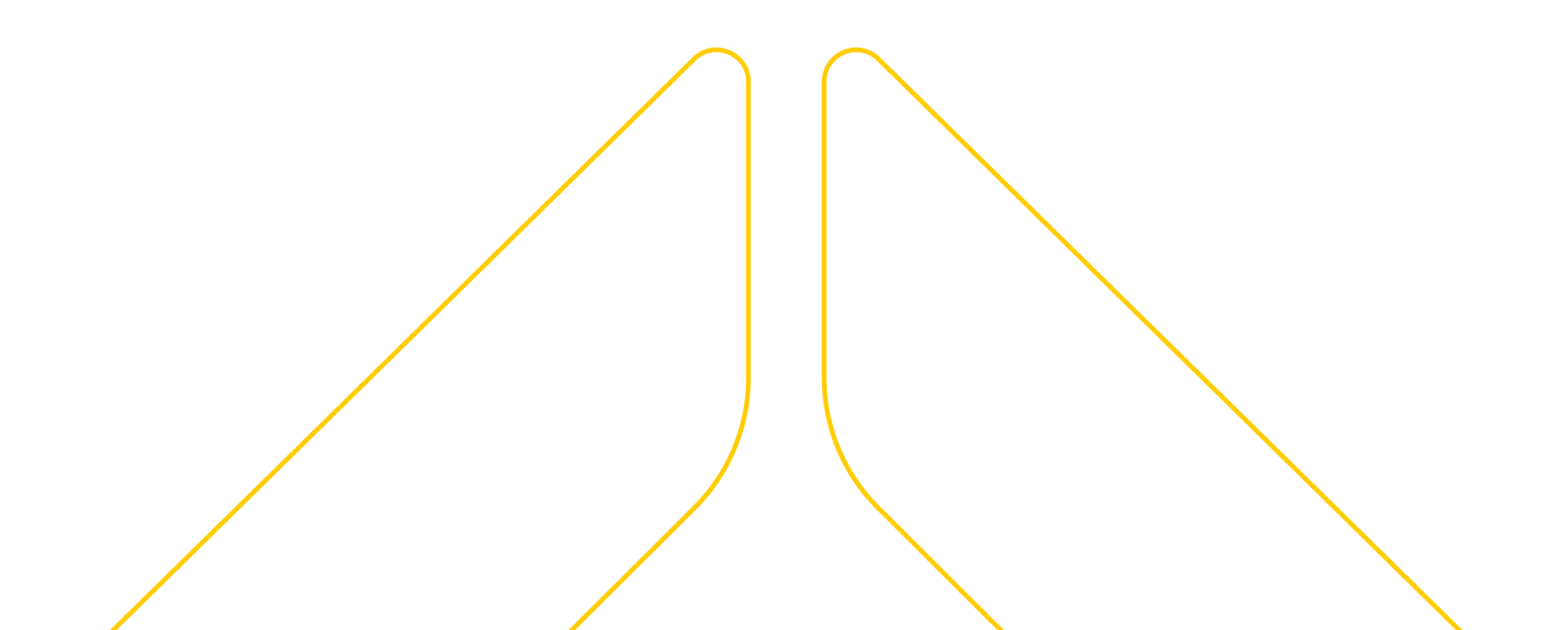
Best-in-class service through entire lifecycle of the machine
By choosing a high-performance machine from Lohia Corp, you choose consistent quality, efficient production, as well as safe and reliable operations. Our goal is to serve you, enhance your operational efficiency and partner you in running your business profitably. With a relentless pursuit of progress, our Service Team provides you a competitive market edge through its swift response time and efficient issue resolution, supported by its hub-based network. With a relentless pursuit of progress, our Service Team provides you a competitive market edge through its swift response time and efficient issue resolution, supported by its hub-based network.
Remote & Digital Services
Training & Performance Optimization
Scheduled Maintenance
System Upgrades & Retrofits
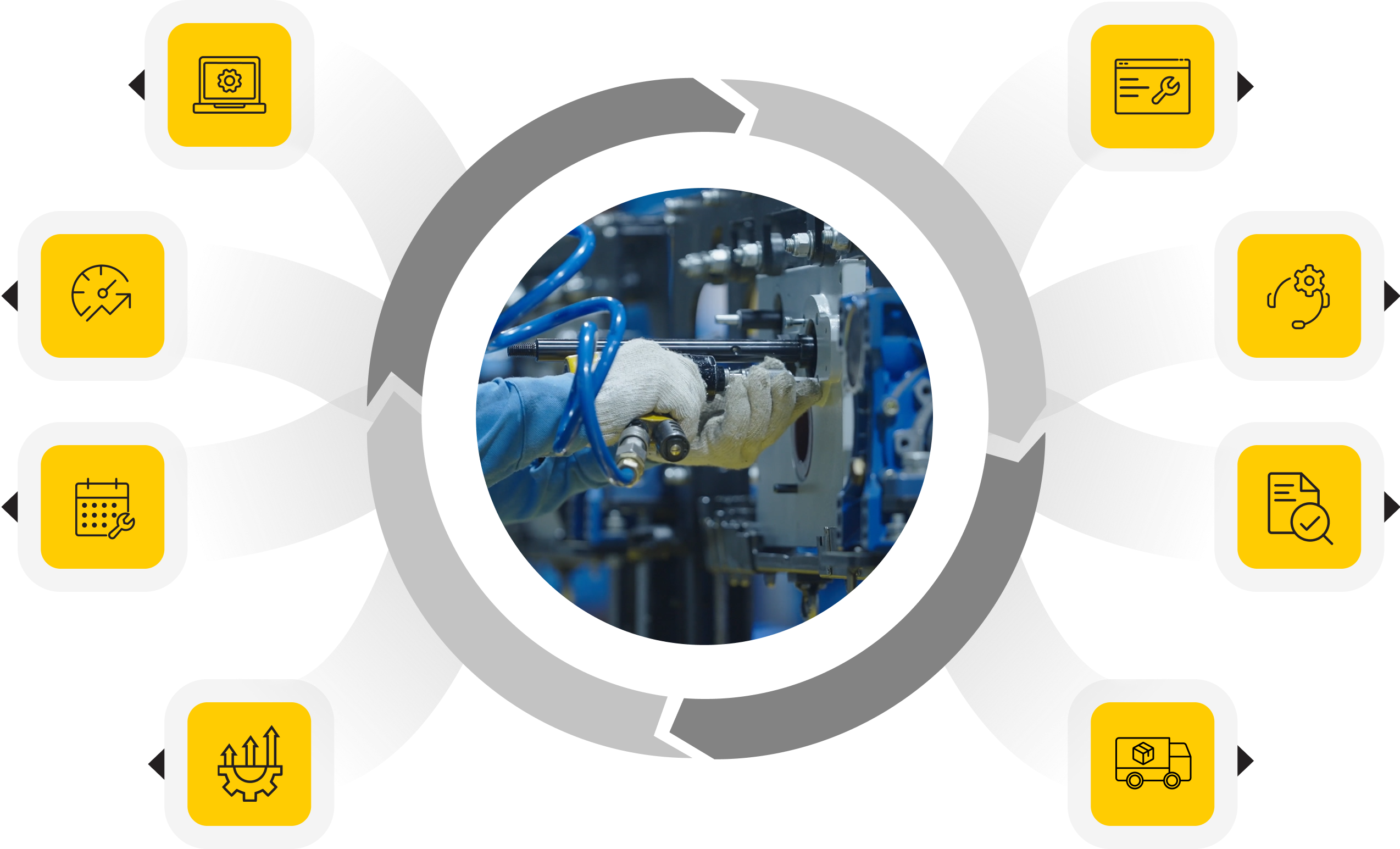
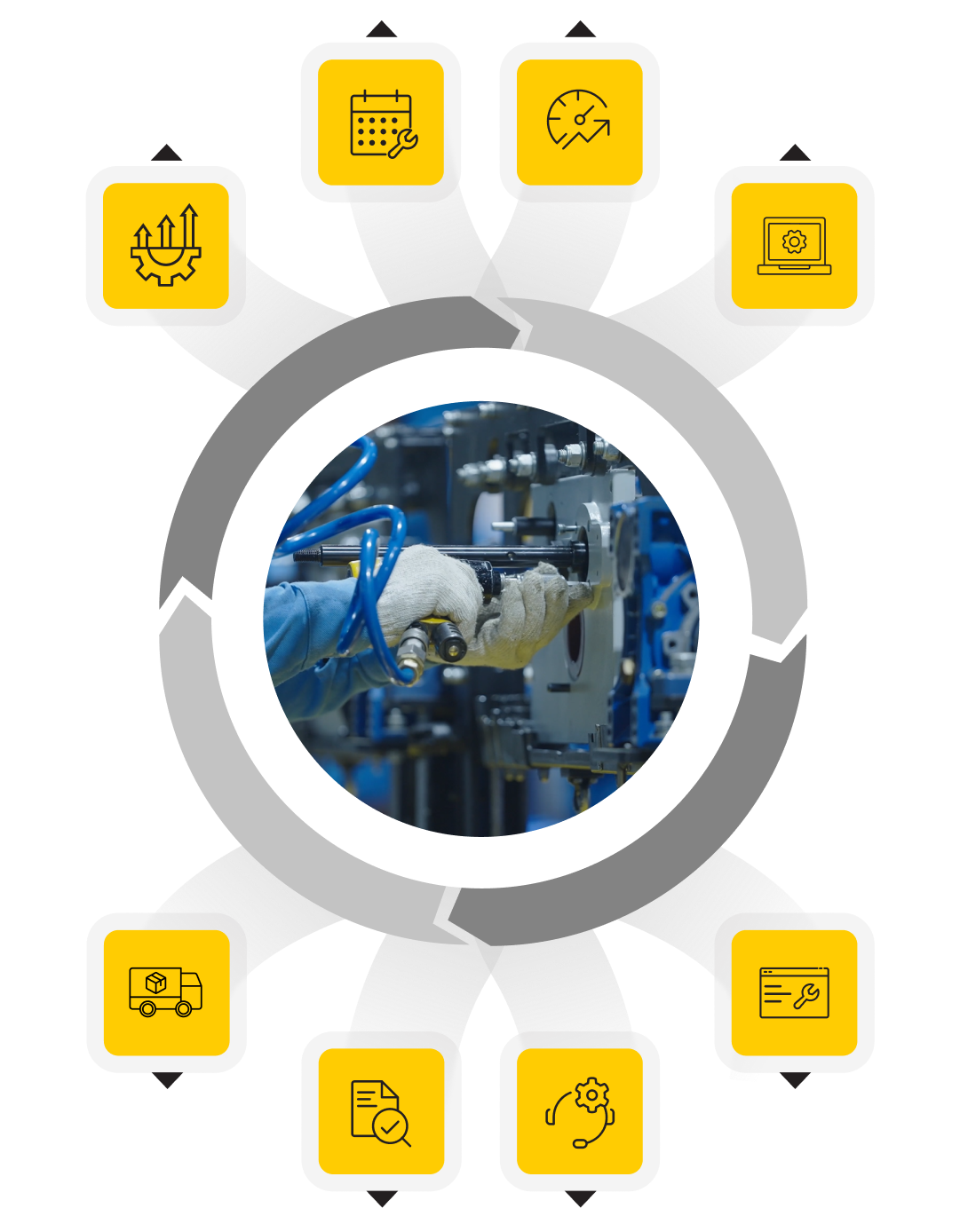
Installation & Setup
Technical Expertise & Support
Audits & Safety Checks
Spare Parts Delivery
The “Lohia Corp difference" in customer service
Our wide ranging solutions for all your needs
End-to-end and proactive customer support
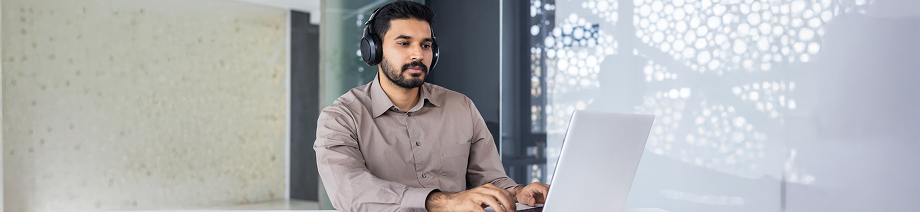
- 115 experienced, proficient and competent service technicians for machine installation and service support
- A dedicated team of professionals in Process and Plant Engineering
- 24/7 access to service experts
Fast response and quick problem resolution with support available by phone, local technician visits, or remote tools
We serve you round-the-clock, around the world
We are committed to provide you support to ensure efficient operation of your manufacturing process. Our experienced service technicians offer expert assistance throughout the machine’s lifecycle, from installation to ongoing maintenance and repairs. We understand that continuous plant operations are critical to efficiency and profitability. Our tailored solutions optimize machine performance, ensuring continuous production. With service experts and quick response time, we help minimize downtime and maintain uninterrupted operations.
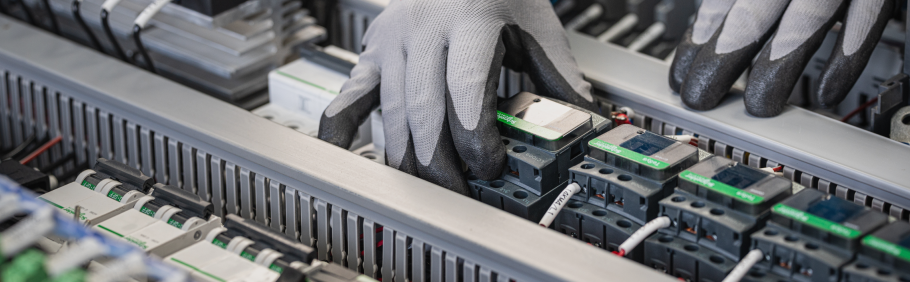
- Machine modernisation to current advanced technology levels by improving existing features and added new
- Extending machinery’s lease of life
- Reducing downtime and resulting in continuous improvement
- Improving overall equipment efficiency (OEE) and restoring machinery to near-new performance
- Integrating with digital innovations seamlessly
- Restore used old Raffia machinery as close to original specifications as possible ensuring proper function
- Validation by LCL Experts for optimum machine availability
- Enabling refurbishment of any machinery
We help you combine continuous improvement and cost efficiency
Machine Rebuilding
Our service experts in Machine Rebuilding and Refurbishment use their vast experience and knowledge to rebuild, modify and upgrade your old machinery, align it with advanced technology and maximise its longevity.
Upgrades
With Lohia Corp upgrades, your machines remain relevant at all times. Our service team is delighted to advise on the right upgrade solution for your machine.
Our system upgrades, wide range of modernisations and complete overhaul of the machinery optimise every single process, improve existing functions, and install new features, resulting in continuous improvement and increased production. This helps you extend the life and efficiency of your machine and lead to targeted performance enhancement.
Retrofits
Our retrofit solutions ensure new functions bring your equipment to state-of-the-art technology. New modules are added to existing Lohia Corp machines. This prepares you well to face the dynamic changes and new challenges in the market.
We also have the expertise in offering customer-specific solutions and modular retrofitting of extrusion lines from other manufacturers. With consulting and installation services, our intensive support extends right till successful commissioning.
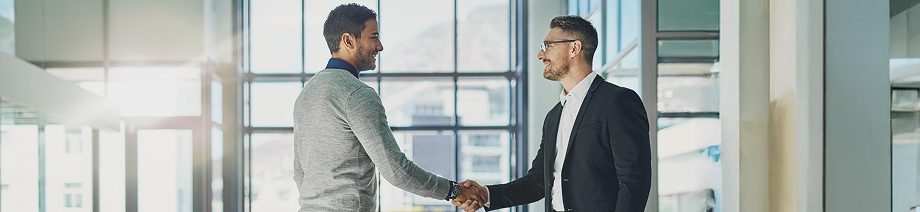
- Flexible and extended warranty & post-warranty services
- Configuring individually adapted maintenance contracts to suit your specific needs
- Systematic maintenance to enhance life of parts and machinery
- Maximising uptime and keeping system healthy and operational
- Reports & Analytics are generated to gain clarity on machine status and interpret important data
Get your programs configured based on your needs
We customise our service contracts to match your specific needs. We configure programs that are individually adapted based on prescribed maintenance of the equipment.
We help you extend your equipment’s lifespan and increase return on investment
You can rely on us to keep your machines operating at peak efficiency with systematic maintenance and expert service support. Regular maintenance is essential to maximizing uptime and optimizing your return on investment. Our systematic maintenance approach extends the life of your machinery, ensuring reliable and efficient performance while reducing the risk of unexpected breakdowns. With a team of experienced field service specialists, we provide proactive solutions that prevent downtime and keep your production running at optimal performance.
Full Maintenance
As part of Full Maintenance contracts on Looms, you gain access to a dedicated Service Engineer, besides coverage of spare parts in scope, with a readily available stock at your own premises. Our flexible and extended warranty and post-warranty services protect you from unexpected repair costs, giving you peace of mind by extending your equipment’s lifespan and increasing your return on investment.
Annual Maintenance
Our Annual Maintenance Contracts (AMC) on Looms and Extrusion Lines guarantees you that our certified experts will periodically service and maintain your equipment. This is aimed at helping you with long-term planning, effective utilisation, and improved productivity.
5S Implementation
We also guide you on 5S implementation within the factory premises through our 5-step process of “Sort, Set in Order, Shine, Standardise, and Sustain”. With this, we help you create a more organised, productive and effective workspace.
Service Reports
Through our Service Reports, our goal is to provide with the most accurate information on the condition of your machine in as clear manner as possible. We deliver improved clarity on the machine’s status to help you identify and monitor trends in support quality and performance management. With a strong focus on providing overall equipment efficiency (OEE), we restore your machinery to near-new performance levels and reduce downtime through seamless digital innovations
Leveraging IOT
By leveraging IoT and gaining real-time data and valuable insights, our innovative solutions optimise your production processes and maintain overall equipment effectiveness of the machine. With integration of IOT, we enable proactive support that helps you improve your functionality and efficiency.
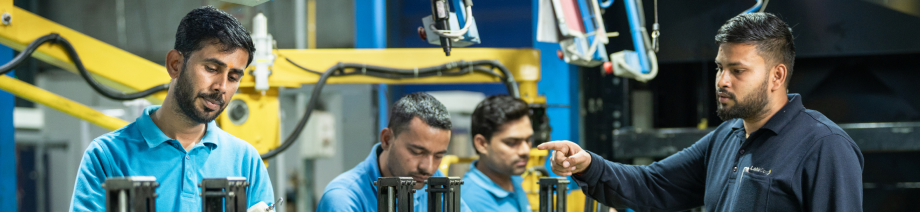
- Onsite training to teach product usage, safety norms and best practices
- Conducting webinars and seminars to cater to diverse needs of customers
- Training on complete plant operations & maintenance
- Guidance on 5S implementation
Learn about product usage, safety and best practices through onsite training
We understand your business is unique, and hence we tailor your training and technical support that is suited to your needs. Our training programs help you boost your process efficiency and employee productivity, and keep pace with the dynamically changing environment.
Lohia Corp’s wide range of professional customer training programs match your employees’ pre-existing knowledge. We adapt the course content to your specific needs with practical hands-on experience to help them efficiently and effectively run our machines and secure competitiveness.
With practical experience and extensive knowhow, our Training Specialists disseminate onsite training on comprehensive product knowledge, specific skills, targeted application device, operations & maintenance, and also on related safety norms for the equipment.
Investment in customer training helps you increase cost savings in your business and enhance safety of your employees. We also conduct seminars and live webinars to update you and help you satisfy your diverse needs.
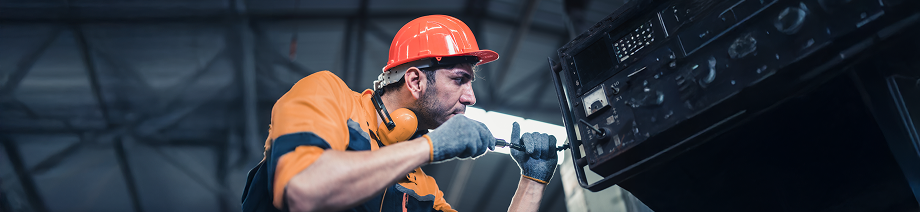
- Factory fitted device facilitates remote access to machines via the Internet at the customers’ site
- Remote access and diagnosis leads to reduced turnaround time and travel cost, and enables increased productivity
- Access to secure, reliable and user-friendly technical support with quick problem-solving and reduced lifecycle costs
Troubleshoot your machine issues efficiently, effectively and remotely
Our Remote Services provide quick and efficient solutions through secure online remote access. Our experts connect directly to your machines, diagnose issues in real time, and troubleshoot faults effectively.
Using live video assistance and factory-fitted diagnostic devices, we help you identify and rectify machine faults quickly and successfully. Our secure and user-friendly support minimizes downtime and ensures seamless machine performance, no matter where you are.
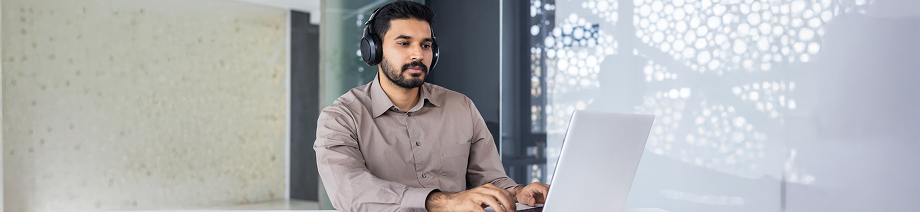
- 115 experienced, proficient and competent service technicians for machine installation and service support
- A dedicated team of professionals in Process and Plant Engineering
- 24/7 access to service experts
Fast response and quick problem resolution with support available by phone, local technician visits, or remote tools
We serve you round-the-clock, around the world
We are committed to provide you support to ensure efficient operation of your manufacturing process. Our experienced service technicians offer expert assistance throughout the machine’s lifecycle, from installation to ongoing maintenance and repairs. We understand that continuous plant operations are critical to efficiency and profitability. Our tailored solutions optimize machine performance, ensuring continuous production. With service experts and quick response time, we help minimize downtime and maintain uninterrupted operations.
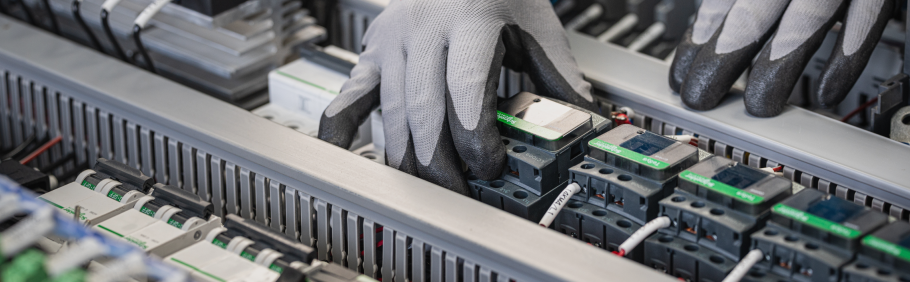
- Machine modernisation to current advanced technology levels by improving existing features and added new
- Extending machinery’s lease of life
- Reducing downtime and resulting in continuous improvement
- Improving overall equipment efficiency (OEE) and restoring machinery to near-new performance
- Integrating with digital innovations seamlessly
- Restore used old Raffia machinery as close to original specifications as possible ensuring proper function
- Validation by LCL Experts for optimum machine availability
- Enabling refurbishment of any machinery
We help you combine continuous improvement and cost efficiency
Machine Rebuilding
Our service experts in Machine Rebuilding and Refurbishment use their vast experience and knowledge to rebuild, modify and upgrade your old machinery, align it with advanced technology and maximise its longevity.
Upgrades
With Lohia Corp upgrades, your machines remain relevant at all times. Our service team is delighted to advise on the right upgrade solution for your machine.
Our system upgrades, wide range of modernisations and complete overhaul of the machinery optimise every single process, improve existing functions, and install new features, resulting in continuous improvement and increased production. This helps you extend the life and efficiency of your machine and lead to targeted performance enhancement.
Retrofits
Our retrofit solutions ensure new functions bring your equipment to state-of-the-art technology. New modules are added to existing Lohia Corp machines. This prepares you well to face the dynamic changes and new challenges in the market.
We also have the expertise in offering customer-specific solutions and modular retrofitting of extrusion lines from other manufacturers. With consulting and installation services, our intensive support extends right till successful commissioning.
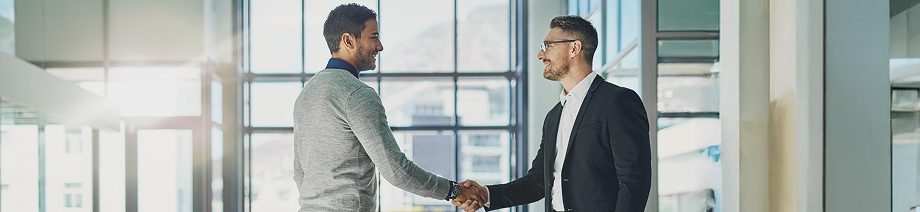
- Flexible and extended warranty & post-warranty services
- Configuring individually adapted maintenance contracts to suit your specific needs
- Systematic maintenance to enhance life of parts and machinery
- Maximising uptime and keeping system healthy and operational
- Reports & Analytics are generated to gain clarity on machine status and interpret important data
Get your programs configured based on your needs
We customise our service contracts to match your specific needs. We configure programs that are individually adapted based on prescribed maintenance of the equipment.
We help you extend your equipment’s lifespan and increase return on investment
You can rely on us to keep your machines operating at peak efficiency with systematic maintenance and expert service support. Regular maintenance is essential to maximizing uptime and optimizing your return on investment. Our systematic maintenance approach extends the life of your machinery, ensuring reliable and efficient performance while reducing the risk of unexpected breakdowns. With a team of experienced field service specialists, we provide proactive solutions that prevent downtime and keep your production running at optimal performance.
Full Maintenance
As part of Full Maintenance contracts on Looms, you gain access to a dedicated Service Engineer, besides coverage of spare parts in scope, with a readily available stock at your own premises. Our flexible and extended warranty and post-warranty services protect you from unexpected repair costs, giving you peace of mind by extending your equipment’s lifespan and increasing your return on investment.
Annual Maintenance
Our Annual Maintenance Contracts (AMC) on Looms and Extrusion Lines guarantees you that our certified experts will periodically service and maintain your equipment. This is aimed at helping you with long-term planning, effective utilisation, and improved productivity.
5S Implementation
We also guide you on 5S implementation within the factory premises through our 5-step process of “Sort, Set in Order, Shine, Standardise, and Sustain”. With this, we help you create a more organised, productive and effective workspace.
Service Reports
Through our Service Reports, our goal is to provide with the most accurate information on the condition of your machine in as clear manner as possible. We deliver improved clarity on the machine’s status to help you identify and monitor trends in support quality and performance management. With a strong focus on providing overall equipment efficiency (OEE), we restore your machinery to near-new performance levels and reduce downtime through seamless digital innovations
Leveraging IOT
By leveraging IoT and gaining real-time data and valuable insights, our innovative solutions optimise your production processes and maintain overall equipment effectiveness of the machine. With integration of IOT, we enable proactive support that helps you improve your functionality and efficiency.
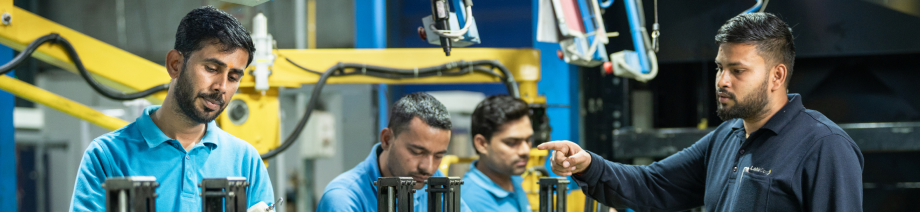
- Onsite training to teach product usage, safety norms and best practices
- Conducting webinars and seminars to cater to diverse needs of customers
- Training on complete plant operations & maintenance
- Guidance on 5S implementation
Learn about product usage, safety and best practices through onsite training
We understand your business is unique, and hence we tailor your training and technical support that is suited to your needs. Our training programs help you boost your process efficiency and employee productivity, and keep pace with the dynamically changing environment.
Lohia Corp’s wide range of professional customer training programs match your employees’ pre-existing knowledge. We adapt the course content to your specific needs with practical hands-on experience to help them efficiently and effectively run our machines and secure competitiveness.
With practical experience and extensive knowhow, our Training Specialists disseminate onsite training on comprehensive product knowledge, specific skills, targeted application device, operations & maintenance, and also on related safety norms for the equipment.
Investment in customer training helps you increase cost savings in your business and enhance safety of your employees. We also conduct seminars and live webinars to update you and help you satisfy your diverse needs.
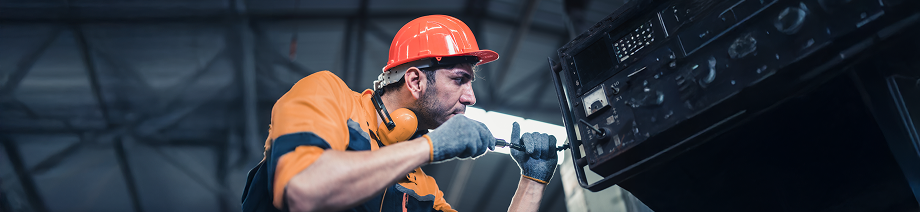
- Factory fitted device facilitates remote access to machines via the Internet at the customers’ site
- Remote access and diagnosis leads to reduced turnaround time and travel cost, and enables increased productivity
- Access to secure, reliable and user-friendly technical support with quick problem-solving and reduced lifecycle costs
Troubleshoot your machine issues efficiently, effectively and remotely
Our Remote Services provide quick and efficient solutions through secure online remote access. Our experts connect directly to your machines, diagnose issues in real time, and troubleshoot faults effectively.
Using live video assistance and factory-fitted diagnostic devices, we help you identify and rectify machine faults quickly and successfully. Our secure and user-friendly support minimizes downtime and ensures seamless machine performance, no matter where you are.